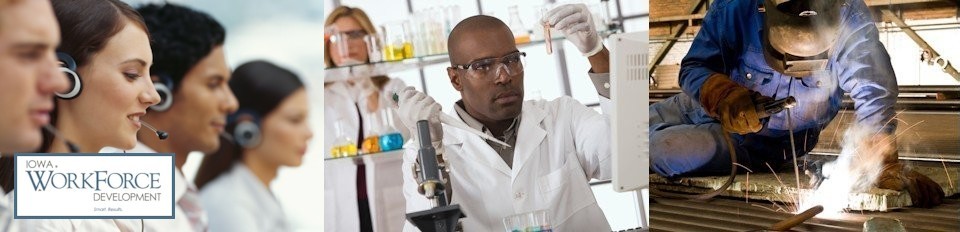
Job Information
Conductix-Wampfler 8Bar - Saflec and Roll Mill Area Set Up and Production in Harlan, Iowa
Conductix-Wampfler is a progressive and growing organization that offers challenging and rewarding opportunities in the electrification and cable management markets. We are looking for a self-directed, dependable, motivated, quality and safety-minded team member for our 8 Bar Machine and Roll Mill Department. WE WILL TRAIN!
In this position, you will assist with set-up, daily production, and scheduling of machines, along with assisting with continuous improvement projects.
EOE/Drug-Free Workplace
Qualified candidates will possess the following:
2-5 years of roll mill/machine set up experience a plus but we are willing to train the right candidate
Ability to read blueprints
Experience in a quality environment
Exhibit problem solving skills
Good communication skills
Conductix-Wampfler offers a great starting wage, with health, dental, and life insurance, 401k plan, paid vacation/personal time and holidays, profit sharing and tuition reimbursement program.
Please send resume to rogene.smith@conductix.com, apply online at www.conductix.us under careers or apply in person at 1605 Industrial Parkway, Harlan, Iowa.
Drug-free workplace/EOE
See full job description below:
SUMMARY
Perform various duties to setup and operate 8-Bar-Saflec processor, cover machine with print number coder and cover cut to length saw for standard bar items, perform various duties to set up and operate curve bar area. Items such as building expansion, curving a variety of 8-Bar, Hevi-Bar, the cutting of wires and handling for special orders. Setup, operate and maintain 8-Bar roll mill, cap roll mill c-track, Cluster Bar roll mill, Safelec 2 roll mill machine, package machine, punch press and cut off dies by performing the following duties.
ESSENTIAL DUTIES AND RESPONSIBILITIES include the following. Other duties may be assigned.
Know capacity and operate forklift and overhead crane. Bridgeport mills, punch press and use a variety of hand tools.
Set up and operate punch presses, drill presses, Bridgeport, saw, sanders, wire strippers, wire cutter, 8-Bar curve machine, C-Channel curve machine and an assortment of hand tools.
Have a good understanding of the operations of air, hydraulics and electrical systems.
Must be able to fix problems involving these systems with minimal supervision.
Complete, schedule and propose preventative maintenance on equipment in this area.
Measure boards using measuring tape, mark cutting lines and saw to required sizes.
Construct pallets, boxes, or crates using staple gun with hammer, nails, and 3/4" Bandar.
Operate table and radial saw.
Operate floor controlled 2-ton overhead crane, transport and position materials by following established procedures and safety rules.
Use chains, grabs, slings and spreader bar to handle materials using care to prevent materials from slipping, dropping, or being damaged during the move.
Thorough knowledge of 8-Bar department workflow.
Perform visual as well as physical inspection of product, raw material, and purchased material to insure quality work.
Select parts and materials with proper identification and location in accordance of engineering blueprint to work order process sheets.
Must involve accurate counting and identification of parts with size, measurement and description.
Read and understand blueprints. Must be able to work from blueprint, work orders, pick list, and verbal or written instructions to perform duties.
Detect and report improper operations, faulty equipment, defective materials and unusual conditions to proper supervisor Read job specifications to determine machine adjustments and material requirement.
Set up and operate machine to punch, cut or process bar. Pushes button or depresses pedal to activate machine.
Observes machine operation to detect defects or machine malfunction.
Measure work piece dimensions to determine accuracy of machine operations.
Perform minor machine maintenance such as oiling machine, dies or work pieces.
Assists machine operators to set up machine and stack, mark, pack and transport finished product.
Use and understand roll forming chart.
Efficient at removing and replacing tooling while inspecting tooling for wear.
Troubleshoot problems with minimal supervision.
Perform visual as well as physical inspection of equipment such as; roll tooling, roller stand, punch press, and cut off dies.
Use various measuring instruments such as; tape, dial calipers, micrometer, square and protractor.
Maintain accurate timecards, work orders and pick lists.
Detect and report improper operations, faulty equipment, defective materials and unusual conditions to proper supervisor.
Maintain work area and equipment in a clean and orderly condition.
Use and follow prescribed safety rules and regulations, lock out/tag out procedures and maintain quality standards.
Find ways to reduce set up and production times.
Must be willing to strive for new ideas, improvements, and quality standards.
Maintains and sustains 5S within the department.
Supports the Quality and EHS policy.
Upholds Core Values.
SUPERVISORY RESPONSIBILITIES
This job has no supervisory responsibilities.
QUALIFICATIONS
To perform this job successfully, an individual must be able to perform each essential duty satisfactorily. The requirements listed below are representative of the knowledge, skill, and/or ability required. Reasonable accommodations may be made to enable individuals with disabilities to perform the essential functions.
EDUCATION and/or EXPERIENCE
High school diploma or general education degree (GED); or one to three months related experience and/or training; or equivalent combination of education and experience.
LANGUAGE SKILLS
Ability to read and interpret documents such as safety rules, operating and maintenance instructions, and procedure manuals. Ability to write routine reports and correspondence. Ability to speak effectively before groups of customers or employees of the organization.
MATHEMATICAL SKILLS
Ability to add, subtract, multiply, and divide in all units of measure, using whole numbers, common fractions, and decimals. Ability to compute rate, ratio, and percent and to draw and interpret bar graphs.
REASONING ABILITY
Ability to apply common sense understanding to carry out detailed but uninvolved written or oral instructions. Ability to deal with problems involving a few concrete variables in standardized situations.
CERTIFICATES, LICENSES, REGISTRATIONS PHYSICAL DEMANDS
The physical demands described here are representative of those that must be met by an employee to successfully perform the essential functions of this job. Reasonable accommodations may be made to enable individuals with disabilities to perform the essential functions.
While performing the duties of this job, the employee is regularly required to stand and use hands to finger, handle, or feel. The employee frequently is required to reach with hands and arms. The employee is occasionally required to walk; sit; stoop, kneel, crouch, or crawl; and talk or hear. The employee must regularly lift and/or move up to 50 pounds, frequently lift and/or move up to 50 pounds, and occasionally lift and/or move up to 25 pounds. Specific vision abilities required by this job include close vision, distance vision, color vision, depth perception, and ability to adjust focus.
WORK ENVIRONMENT
The work environment characteristics described here are representative of those an employee encounters while performing the essential functions of this job. Reasonable accommodations may be made to enable individuals with disabilities to perform the essential functions.
While performing the duties of this job, the employee is regularly exposed to moving mechanical parts. The employee is occasionally exposed to wet and/or humid conditions, fumes or airborne particles, and vibration. The noise level in the work environment is usually moderate.
COMPETENCIES NEEDED TO PERFORM THIS POSITION
Analytical - Able to read blueprints; Able to follow workflow processes and procedures and make suggestions for improvement; Use measuring instruments; Determine correct tolerance.
Design - Generate creative solutions; Use feedback to modify designs; Demonstrates attention to detail.
Problem Solving - Identifies and resolves problems in a timely manner. Develops alternative solutions; Works well in group problem-solving situations; Can identify print errors and work to make the needed corrections.
Project Management - Communicates changes and progress; Completes projects on time; Participates in team activities.
Technical Skills - Pursues training and development opportunities; Strives to continuously build knowledge and skills; Shares expertise with others; Handles the technical aspects of their duties.
Customer Service - Responds promptly to customer needs; Meets commitments.
Interpersonal Skills - Focuses on resolving conflict, not blaming; Remains open to others' ideas and tries new things.
Oral Communication - Responds well to questions; Participates in meetings.
Written Communication - Able to read and interpret written information.
Teamwork - Exhibits objectivity and openness to others' views; Gives and welcomes feedback; Contributes to building a positive team spirit; Puts the success of the team above own interests.
Leadership - Exhibits confidence in self and others; Accepts feedback from others.
Quality - Looks for ways to improve quality; Demonstrates accuracy and thoroughness; Looks for ways to improve and promote quality; Applies feedback to make improvements.
Business Acumen - Displays orientation to profitability.
Cost Consciousness - Develops and implements cost-saving measures.
Meeting Preparation - Comes prepared for each meeting; Completes assigned tasks; Participates in meetings.
Diversity - Promotes a harassment-free environment.
Ethics - Treats people with respect; Keeps commitments.
Organizational Support - Follows policies and procedures; Supports organization's goals and values.
Motivation - Sets and achieves challenging goals; Demonstrates persistence and overcomes obstacles.
Planning and Organizing - Prioritize and plans work activities; Uses time efficiently.
Professionalism - Approaches others in a tactful manner; Treats others with respect; Accepts responsibility for own actions; Follows through on commitments.
Quantity - Meets productivity standards; Completes work in a timely manner; Works quickly.
Safety and Security - Observes safety and security procedures; Reports unsafe conditions or practices; Uses equipment and material properly.
Adaptability - Adapts to changes in the workplace; Able to deal with frequent change, delays, or unexpected events.
Attendance/Punctuality - Is consistently at work and on time; Ensures responsibilities are covered when absent; Arrives at meetings and appointments on time.
Dependability - Follows instruction; Keeps commitments; Completes tasks on time or notifies appropriate person with an alternative plan.
Initiative - Volunteers readily; Undertakes self-development activities; Seeks increased responsibility; Looks for opportunities; Asks for and offers help when needed.
Innovation - Displays creative thinking; Generates suggestions for improvements.